Selecting a suitable punch case material is a critical decision in the manufacturing of fasteners such as bolts, screws, studs, and nuts. The punch case plays a protective and supportive role for the punch during the cold or hot forging process, ensuring dimensional stability, reducing wear, and absorbing impact loads. The right choice of material can significantly enhance tool life, maintain product consistency, and reduce downtime caused by frequent maintenance or tool failure.
Below is a detailed and professional discussion on how to select a suitable punch case material for fastener production, considering mechanical, thermal, and operational factors.
1. Understand the Function of the Punch Case
- Provides structural support to the punch core, absorbing radial and axial stresses during forging.
- Prevents punch fracture due to uneven stress distribution.
- Protects from deformation caused by repeated impact and compressive forces.
- Maintains concentric alignment of the punch, ensuring dimensional accuracy of fasteners.
- Acts as a thermal barrier in hot forging applications, where thermal fatigue is a concern.
Thus, the material needs to have a combination of high toughness, wear resistance, good machinability, and—when required—thermal stability.
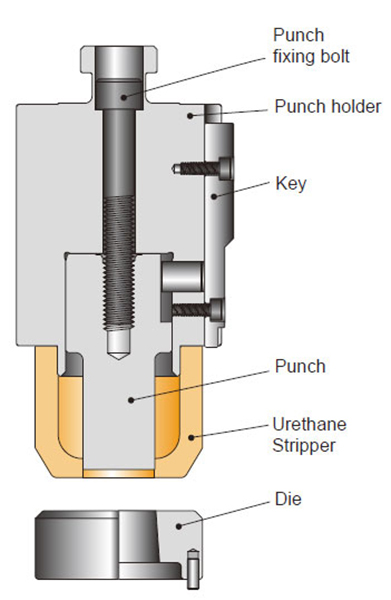
2. Key Factors in Material Selection
A. Strength and Toughness
- The material must withstand high compressive loads without cracking.
- Toughness is essential to prevent brittle fracture due to sudden impact or cyclic loading.
- The ideal material should have a balanced hardness (around HRC 40–50 after treatment), not so hard that it becomes brittle, and not so soft that it wears prematurely.
B. Wear Resistance
- Due to the abrasive environment and high-pressure contact with other tooling and the workpiece, the material should have good wear resistance.
- This is especially critical when forming high-strength fasteners or working with abrasive materials like stainless steel.
C. Thermal Properties
- In hot forging or warm heading, the punch case material should withstand elevated temperatures without losing hardness (tempering resistance).
- Thermal fatigue resistance is important to avoid micro-cracking and surface scaling.
D. Machinability and Treatability
- Ease of machining is important for manufacturing accuracy and reducing production costs.
- The material should also respond well to heat treatment, especially through hardening and tempering, to fine-tune the hardness and toughness.
3. Commonly Used Materials for Punch Cases
Here are some typical materials used in punch case manufacturing, along with their characteristics:
A. DIN 1.2344 / H13 (Hot Work Tool Steel)
- Properties: High toughness, excellent thermal shock resistance, good wear resistance, and good hardenability.
- Applications: Widely used in both cold and hot forging punches and cases.
- Pros: Good resistance to thermal cracking, good machinability.
- Note: Suitable for both cold heading and warm/hot forging applications.
B. SKD61 (Japanese Equivalent of H13)
- Properties: Similar to DIN 1.2344; high strength at elevated temperatures, wear and impact resistance.
- Applications: Hot forging dies, punch holders, extrusion dies.
- Pros: Reliable performance under cyclic thermal and mechanical loads.
C. DIN 1.2714 (45NiCrMo16)
- Properties: High toughness and good wear resistance; capable of being oil-hardened.
- Applications: Large-size punch cases, hot forging dies.
- Pros: Maintains hardness under high loads; suitable for shock-prone applications.
D. DIN 1.2767 (45NiCrMo16 + Higher Carbon)
- Properties: High tensile strength, very high toughness.
- Applications: Cold heading punch cases for large diameter fasteners.
- Pros: Very resistant to cracking; used in demanding cold forming.
E. AISI 4140 / 42CrMo
- Properties: Medium-hardness, chromium-molybdenum alloy steel.
- Applications: General-purpose punch holders and cases.
- Pros: Economical, good balance of hardness and toughness, easy to machine and treat.
- Note: Often used in less severe applications or in combination with inserts.
4. Heat Treatment Considerations
The performance of punch case materials depends heavily on proper heat treatment, which adjusts the internal structure for enhanced toughness and wear resistance. General guidelines:
- Preheat to reduce thermal stress during quenching.
- Oil or air quenching, depending on the material and section thickness.
- Tempering to achieve the desired final hardness (usually HRC 40–50 for cases).
- For H13/SKD61: Double tempering is recommended to stabilize the structure and reduce retained austenite.
5. Match Material to Application Scenario
Application Type | Recommended Material | Notes |
Cold heading of carbon steel | DIN 1.2714, AISI 4140 | Moderate load, good toughness |
Cold heading of stainless steel | DIN 1.2767, SKD61 | Needs higher wear and crack resistance |
Hot forging bolts | H13 / SKD61 | Thermal resistance is critical |
High-speed production | SKD61, DIN 1.2344 | Requires dimensional stability and wear resistance |
Large fasteners (M24+) | DIN 1.2714, DIN 1.2767 | Focus on toughness and structural strength |
6. Additional Considerations
- Coatings (e.g., TiN, CrN) can be applied to increase surface hardness and reduce friction.
- Assembly clearance between punch and case should be optimized to avoid internal stresses.
- Manufacturing tolerance should ensure precise fit with the punch body to reduce stress concentration.
Conclusion
Selecting the right punch case material involves a careful balance of mechanical strength, wear resistance, thermal stability, and manufacturing feasibility. Materials like H13/SKD61, DIN 1.2714, and DIN 1.2767 are industry favorites due to their proven performance in demanding environments. However, the final choice should be based on the specific forming application, workpiece material, production speed, and cost considerations.
By aligning material properties with operational demands, manufacturers can extend tool life, ensure product consistency, and reduce total tooling costs.