In the fast-paced world of metal fastener manufacturing, efficiency, precision, and cost-effectiveness are non-negotiable. Nut Forming Dies play a pivotal role in shaping raw bar stock into finished nuts, ensuring consistent geometry, tight tolerances, and high throughput. Whether you’re producing hex nuts, lock nuts, or specialty profiles, the right forming die design can make all the difference between smooth operations and frequent downtime.
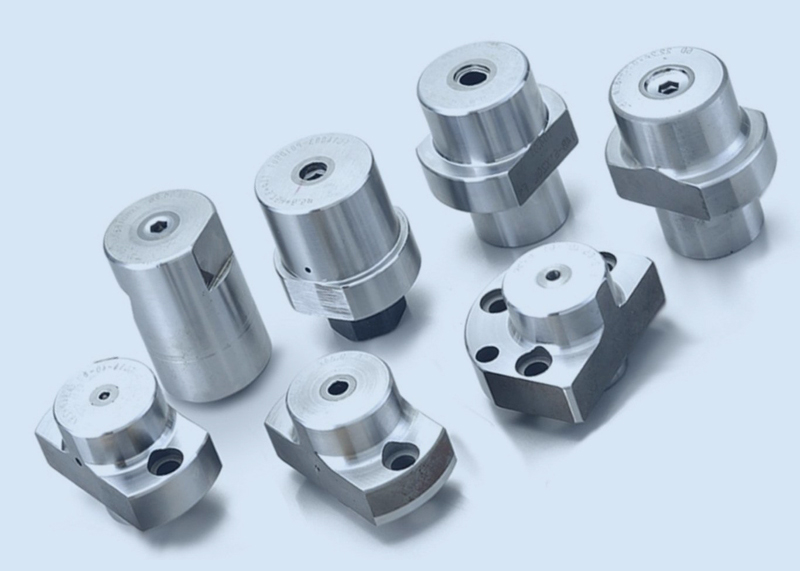
What Are Nut Forming Dies?
Nut Forming Dies are specialized tooling components used in cold-forming or hot-forging processes to produce nuts from metal blanks. These dies consist of two matched halves—often referred to as the punch (upper die) and the cavity (lower die)—which together shape the workpiece under high pressure:
Punch (Upper Die): Shapes the outside profile and cuts any excess material.
Cavity (Lower Die): Defines the internal thread form and final nut dimensions.
By carefully controlling material flow, these dies can produce nuts with minimal flash, precise threads, and excellent surface finish.
Key Benefits of Using Nut Forming Dies
High Throughput: Cold forming with precision dies can reach tens of thousands of pieces per hour, significantly outpacing machining methods.
Material Savings: Forming requires less raw material than traditional machining, as there’s minimal chip waste.
Consistent Quality: A well-designed die ensures uniform dimensions, reducing rejected parts and downstream inspection costs.
Enhanced Mechanical Properties: Work hardening during cold forming can improve nut strength and fatigue life.
Lower Tooling Costs: Although initial die investment can be substantial, the per-part tooling cost declines dramatically at high volumes.
Types of Nut Forming Dies
Depending on production volume, nut geometry, and material, you may choose from several die types:
Die Type | Typical Use Case |
---|---|
Two-Die Sets | Standard hex/hex flange nuts; moderate volume |
Multi-Stage Progressive Dies | Complex profiles; ultra-high volume |
Hot Forging Dies | High-strength alloys; large-diameter nuts |
Combination Thread-Forming Dies | Integrated punching and thread rolling |
Nut Forming Dies can also be customized for non-standard profiles, integrated depressions, or unique locking features (nylon inserts, serrations).
Material Selection for Dies
Die material directly influences tool life, maintenance schedules, and part quality. Common materials include:
High-Speed Steel (HSS): Balances toughness and wear resistance; ideal for lower-volume runs.
Powdered Metal Tool Steel: Offers superior wear resistance and toughness; suited for medium to high volumes.
D2 or AISI H13: Exceptional hardness and hot-work capability; used for hot forging applications.
Special Coatings (TiN, CrN): Reduce galling and extend die life when running stainless steels or abrasive alloys.
Selecting the right grade involves evaluating run length, blank material, lubrication, and operating temperature.
Designing Nut Forming Dies: Best Practices
Dimensional Tolerances: Establish critical tolerances for thread OD, height, and flats width to ensure compatibility with mating bolts.
Draft Angles & Chamfers: Incorporate small draft angles (0.5°–2°) to facilitate die entry and ejection. Chamfers aid in initial material alignment.
Flash Control: Design flash grooves to collect excess material, preventing flash buildup that can damage dies.
Die Alignment Features: Include guide pins and bushings to maintain precise registration between punch and cavity.
Clearance & Lubrication: Ensure adequate die clearance (usually 6%–8% of blank diameter) and specify proper lubricant delivery channels to reduce friction and wear.
A detailed Computer-Aided Design (CAD) model, backed by Finite Element Analysis (FEA), can predict material flow and identify potential stress concentrations before die manufacturing.
Maintenance and Die Care
Regular maintenance is essential to maximize the life of your Nut Forming Dies:
Daily Inspection: Check for chipping, cracks, and excessive wear on punch noses and cavity edges.
Periodic Polishing: Lightly polish die surfaces to remove minor scratches and prevent fretting corrosion.
Lubrication System Checks: Verify that oil jets or grease fittings deliver consistent lubrication to critical die zones.
Regrinding & Recoating: Schedule die regrinding when thread forms deviate beyond tolerance. Reapply PVD coatings as needed to restore surface hardness.
Spare Die Inventory: Maintain a backup set to minimize downtime during maintenance cycles.
Implementing a die maintenance log—tracking run lengths, repair dates, and performance metrics—helps forecast when replacements or refurbishments will be required.
Applications and Industries
Nut Forming Dies serve a wide range of sectors:
Automotive & Heavy Equipment: Production of high-strength nuts for engine blocks, chassis assemblies, and wheel hubs.
Construction & Infrastructure: Hex nuts and coupling nuts for structural steel, scaffolding, and utility installations.
Electronics & Appliances: Miniature nuts for precision assemblies in consumer electronics.
Oil & Gas: Specialty lock nuts and heavy hex nuts for high-pressure flanges and subsea equipment.
Each application may impose unique requirements on surface finish, mechanical properties, or environmental resistance—necessitating specialized die designs.
Nut forming dies are the backbone of efficient, high-quality nut production across countless industries. By selecting the right die type, material, and design features—and by maintaining your tooling with diligence—you can achieve outstanding productivity, reduced costs, and superior fastener performance. Whether you’re scaling up for mass production or tackling specialty nut profiles, investing in expertly engineered Nut Forming Dies is a decision that pays dividends in reliability and profitability.